Lead researchers (Anton Good, Malte Raube, Alexandre Janot, Dr. Bartosz Nowak (L-R)) show off the mini-torsion testing rig controlled with purpose built software for precision torque measurements as a function of insertion depth.
The apparatus will be used to measure the torque required to surgically insert Mg-based screws and plates into bone for fixation applications. The apparatus will assist with the robust design and manufacture of orthopedic implants, paving the way for a new generation of biodegradable magnesium-based medical devices.
“Currently, we have unique suite of capabilities in NZ of being able to produce our own experimental magnesium alloys, thermomechanically process them, and then fabricate them into medical devices, all within the walls of the mechanical engineering laboratories. Torsion testing is just another notch in our belt of capabilities that set us apart on the NZ stage and further afield,” A/Professor Mark Staiger says.
The new torsion testing apparatus is just one of many innovations that the ORTHOMAG group has generated over the last few years, in addition to unique capabilities around synthesis of new magnesium alloys, secondary processing of magnesium alloys using hot rolling and extrusion, and a newly built manufacturing facility for fabricating new orthopedic devices used in our testing campaigns.
“We are also very excited about the advanced computational models we are developing for prediction of the in vivo mechanical performance and degradation of the devices”, Dr. Bartosz Nowak says.
The work is one more step toward making biodegradable metallic implants a potential new industry for New Zealand.
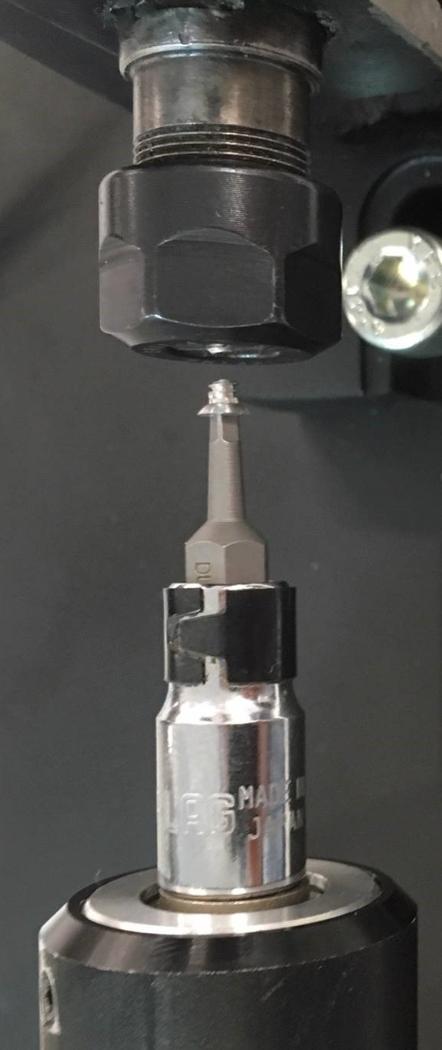